Since the brushless DC motor is used to run the loads at the desired speed , controlling its speed is essential with suitable controller. By controlling the applied voltage, we can run the DC motor at the base and below-rated speeds, whereas by flux weakening above rated. By controlling the speed of the motor , you can vary the speed of the motor according to the requirements and can get the required operation. DC motor speed control is one of the most useful features of the motor. Our speed controllers are available in chassis, NEMA 4X, and digital enclosures.
Our brushless motor and control packages are designed to work together to provide optimal performance. Speed control of BLDC motor is essential for making the motor work at desired rate. Speed of a brushless dc motor can be controlled by controlling the input dc.
All models can be custom designed for 12V or 24V power supply, and the rated speed can be designed. The brushless DC (BLDC) motor is becoming increasingly popular in sectors such as automotive (particularly electric vehicles (EV)), HVAC, white goods and industrial. An electronic speed control or ESC is an electronic circuit that controls and regulates the speed of an electric motor. It may also provide reversing of the motor and dynamic braking. Rotational Speed -Torque characteristics of a brushless DC.
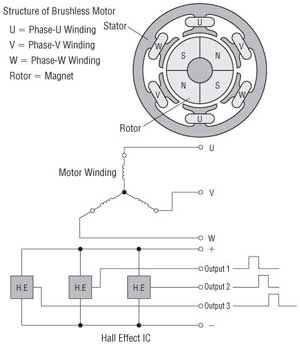
When driving a brushless DC motor , which parameters control the speed. Is it the current in the windings, the voltage, or both? What determines the maximum speed ? Intelligent motor control electronics. All speed and position controls are specially designed for DC motors and brushless DC motors with up to 7W.
Our brushless DC motor drives include power supply solutions for control electronics and gate drivers to enhance efficiency. Due to the integrated current limiting, the drives are protected against thermal overload. Speed Control Systems are preconfigured ex works for the respective motor.
There is even a controller with independent voltage and speed controls so you can discover your motor ’s char- acteristics empirically. Find Expert Advice on About. Here you can find solutions for your motor control project whether you are using brushed DC , stepper , brushless DC , permanent magnet synchronous , AC induction , or switched reluctance motors. Includes in depth information on this motor type and how to control them. Order from our online store today.
Motor Control and Drive Overview Welcome to the Motor Control and Drive design center. Why use a DC motor controller ? Any time there is one active high side mosfet and one active low side mosfet, that means always there is one active PWM pin (Arduino pin or 6). The controller provides pulses of current to the motor windings that control the speed and torque of the motor. The advantages of a brushless motor over a brushed motor are the high power to weight ratio, high speed , and electronic control. Electronic speed controller.
KNACRO DC 5V-12V BLDC DC Brushless Motor Driver Stepless Speed Regulator Controller Reverse voltage protection Over current protection Easily wiring Voltage 5-12V can. Brushless dc (BLDC) motors are preferred as small horsepower control motors due to their high efficiency, silent operation, compact form, reliability, and low maintenance. Motor speed , then, depends upon the amplitude of the applied voltage. Matching a brushless DC motor to a speed controller for your RC airplane always requires you to keep a few important things in mind. Match a brushless DC motor to a speed controller for your RC.
Then check out this outstanding single chip PWM motor speed controller circuit that will give you a complete 3degrees of continuously varying motor speed control right from zero to maximum. The speed is controlled through an externally applied varying DC voltage source. The most striking feature of this circuit is its ability to provide full torque even at minimum motor speeds.
No comments:
Post a Comment
Note: Only a member of this blog may post a comment.